Continuous Improvement: Using a Daily Gemba or Shop Floor Walk
Posted on by William Hazard
One of the most powerful organizational tools for operational management is the Daily Shop Floor or Gemba Walk. This is a critical component of having an effective operational management system. If this is done effectively it sets a great foundation for effective management and a structure for continuous improvement.
A Gemba or Shop Floor Walk is a daily shop floor review where prior days performance to plan is reviewed by the entire leadership team. This does not happen sitting in a conference room - this happens by going to the Gemba or Shop Floor. The structure of the meeting is centered around Plan-Do-Check-Act (PDCA) where there are clear targets. The design of the meeting is for area leadership to report out on prior days performance and did they achieve their targets for Safety, Quality, Delivery, Cost, and Morale.
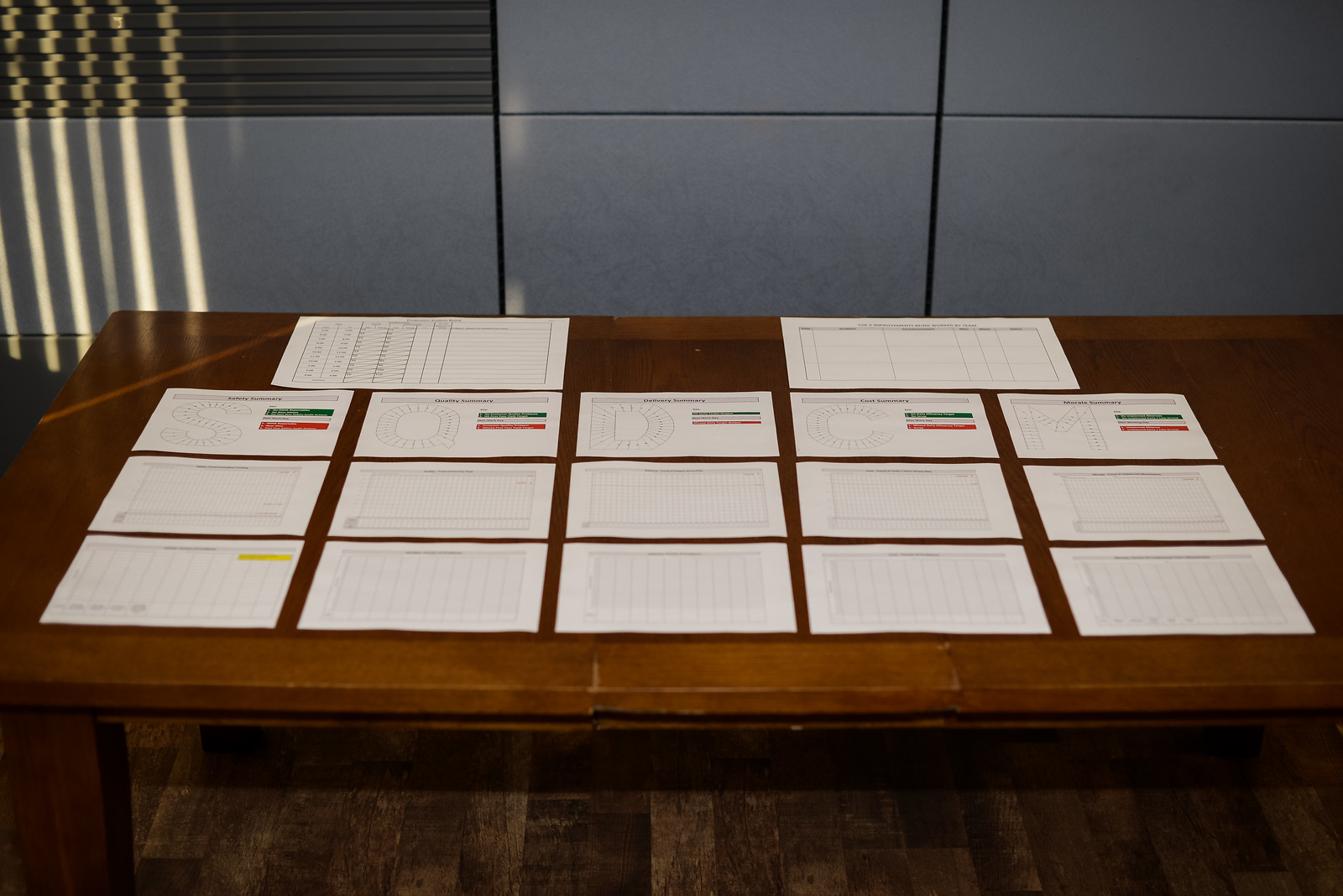
The Daily Gemba or Shop Floor Walk is powerful in many ways:
- Sets very clear targets and measures performance versus these targets. It is human nature to want to win and my teams do not like to report out that they lose!
- Gives clarity to Team on expectations.
- Gives area leadership ownership as they report out daily on performance.
- Helps leadership think strategically as they are responsible to summarize problems and develop a strategy to improve. This becomes foundation for a Continuous Improvement culture.
- Creates a balanced approach around Safety, Quality, Delivery, Cost, and Morale (Can be customized to your preferred design – Key point is it incorporates a balanced approach)
- Creates a common understanding of the problems for all levels of the organization.
- Gets entire leadership team on the shop floor to understand problems and can be used to drive accountability of leadership in getting the problems addressed.
- Assigns clear actions to all functional areas to help solve probems and improve operational performance.
This is just a subset of benefits and usually you will see an immediate performance impact through just measuring. A very true saying: “What gets measured – gets done!”
Our shop floor meeting starts at shipping which is closest to our customer. We review the status of orders for each value stream to insure alignment between Sales, Operations, Customer Service, and support organizations. This is very valuable in insuring alignment and understanding if there are any areas that we are at risk of missing.
We then go to each Value Stream Board where area leadership will report out on performance. They have daily targets for Production using a Production Analysis Board, Safety, Quality, Delivery, Cost, and Morale. There is a binary Red / Green for hitting targets, a trend to show performance over time, a living pareto of issues impacting performance, and a Top 3 Items that the Team is working to improve. There are other tools that can be worked into this including an area Strategy A3, Problem Solving, Accountability Board, Layered Process Audit or others depending on the challenges and management capability. Often keeping it simple is the best.
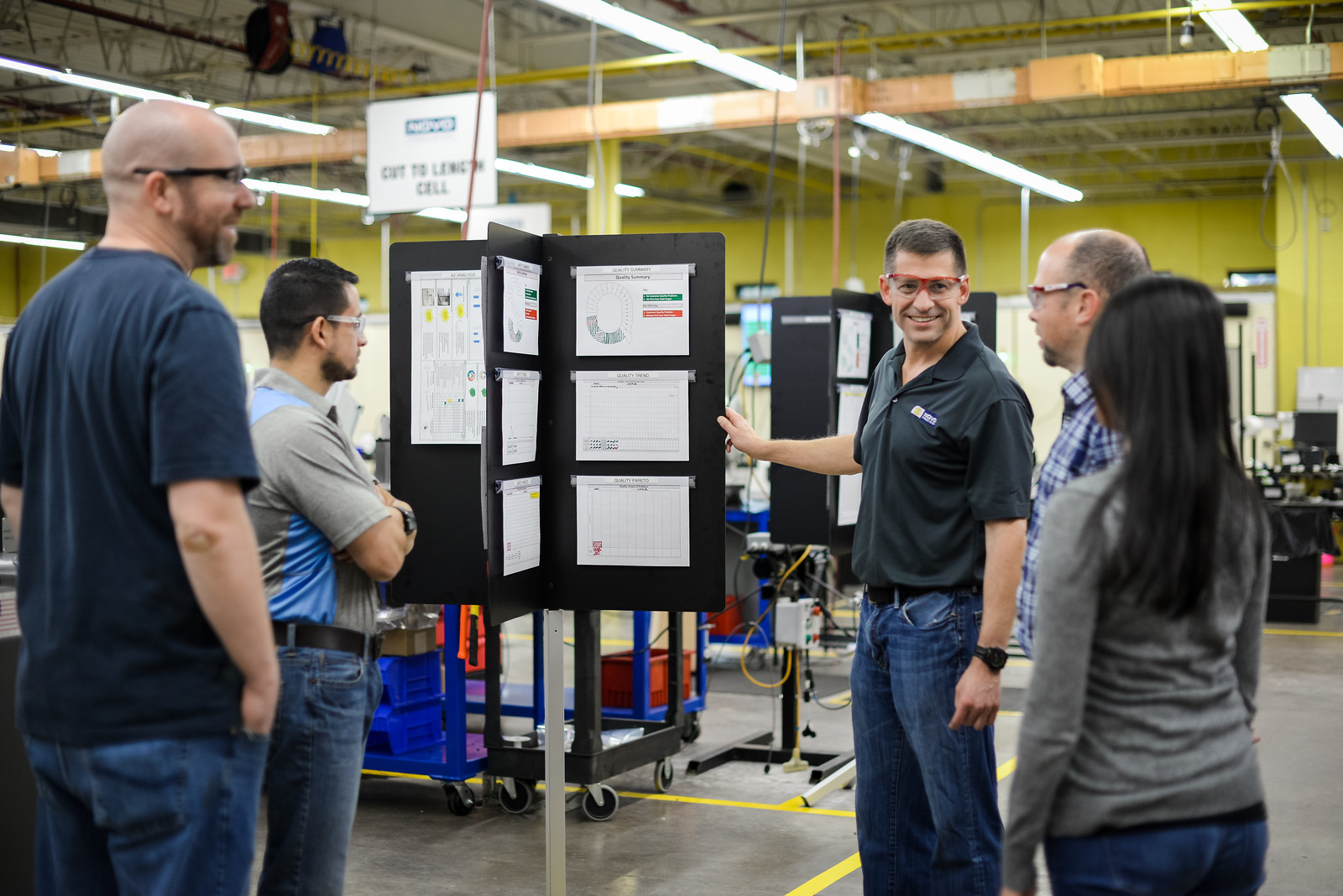
Utilizing the Visual Management Board in Gemba Walk
Having run over a dozen businesses and consulting with 50+ companies we have developed and refined a standard approach for how to do a Gemba or Shop Floor Walk. I encourage you to create and evolve your own process.
One of the challenges in starting this is how to setup a visual management board and what metrics do you start to measure. We have designed and developed a standard visual management board at every company which takes a lot of time and resources.
To simplify this process, we have developed a standard visual management too that we call the Lean Metrics Stand. I would recommend you look at this as an option as it looks very professional and is a very cost-effective solution. We also include all the Templates to get started.
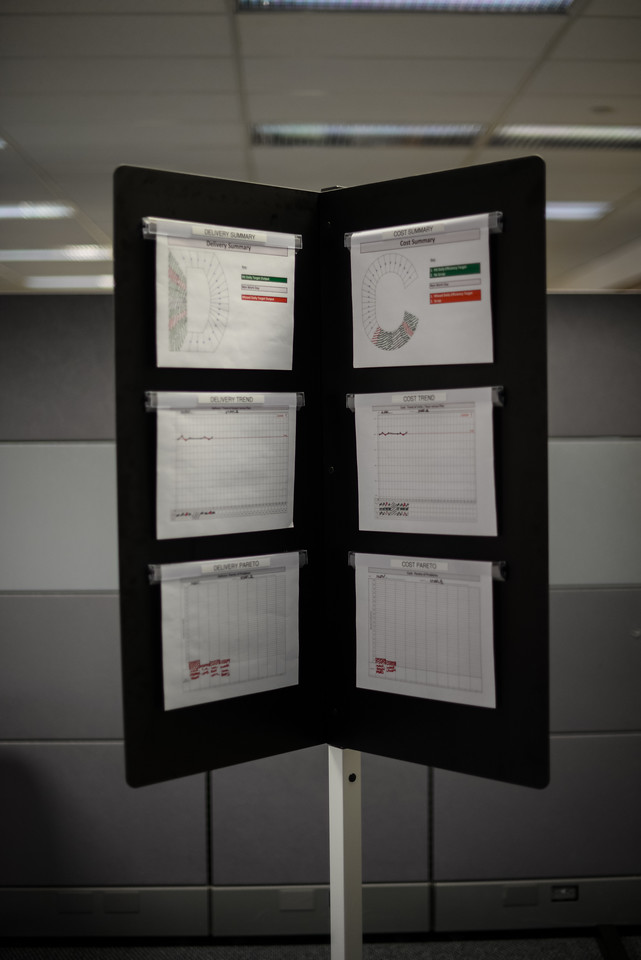
Check out the first blog in our series: Lean Management: What is Operational Cadence?
For more information on our Lean Metric Stands please click here