Lean Metrics Stand
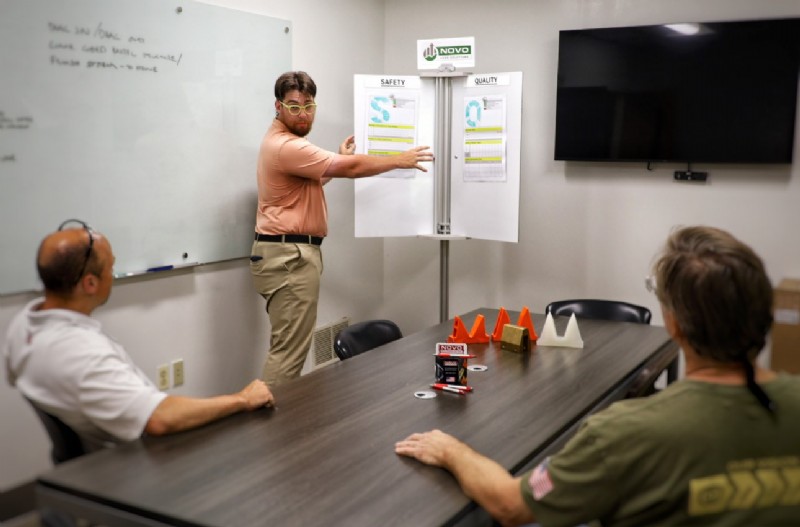
Overview
The right information. In the right place. At the right time. In a simple, straight-forward format to guide decision-making.
It's the soul of Lean Manufacturing, and Novo Precisions Lean Metric Stands can help. Our Lean Metric Stands deliver information on the shop floor, when and where your team needs it. Easy to update, with standard graphic templates....our Metric Stands will help you deliver results!
The Lean Metrics Stand from Novo Precision is a turnkey system to support your Daily Operational Management. This durably constructed, small footprint metrics stand is meant to be on your shop floor right at the process. The Lean Metrics Stand gets your team engaged with a standard set of metrics around Safety, Quality, Delivery, Cost, and Morale tracked daily and to provide transparency to all your team members. Give us a call for pricing including our volume price breaks.
Testimonials:
"I find the Lean Metrics Stands to be a great tool for me as a manager. If there is a problem I can clearly see it and there is a clear explanation by the team. If a line does not hit its daily goal there is a clear, real time explanation as to why. If the problem becomes chronic we can address the issue and fix it. There were times in the past when a line may have an ongoing mechanical issue which became a normal part of operation and eroded our efficiency. The Metrics Boards eliminate that from happening.
The operators have embraced the boards as well. They see their daily goals and do all they can to achieve them. If they exceed them they are proud and show it off. It’s helping them to work better as a team as the goals are clear for all to see."-Skip Griffin-Director of Operations-Metal Finishing Technologies
Visit Our Lean Solutions Blog:
For a better understanding of how to use these boards visit our blog:
- Blog 1-Management Cadence
- Blog 2- Shop Floor or Gemba Walk
No Walls No Worries
Efficient and professional method of presenting information on your shop floor or in an office. Make crucial
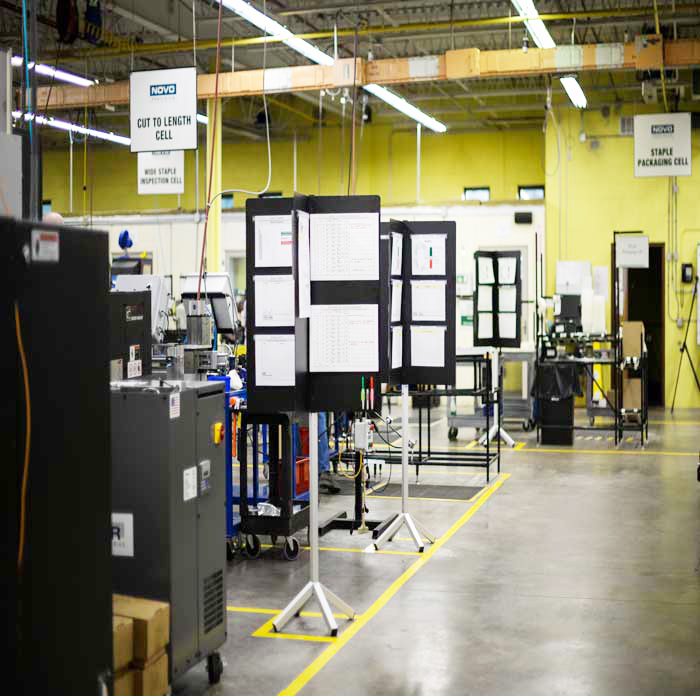
data and key performance indicators visual!
What Gets Measured Gets Done
It's an age old adage but one that is as true today as ever. The Lean Manufacturing Metrics Stand comes stocked with key metrics and interactive graphing to help show trends and highlight opportunities for your team to focus.
Supports Gemba or Shop Floor Management Walk
This is a very professional information stand that can be used to effectively present information or metrics
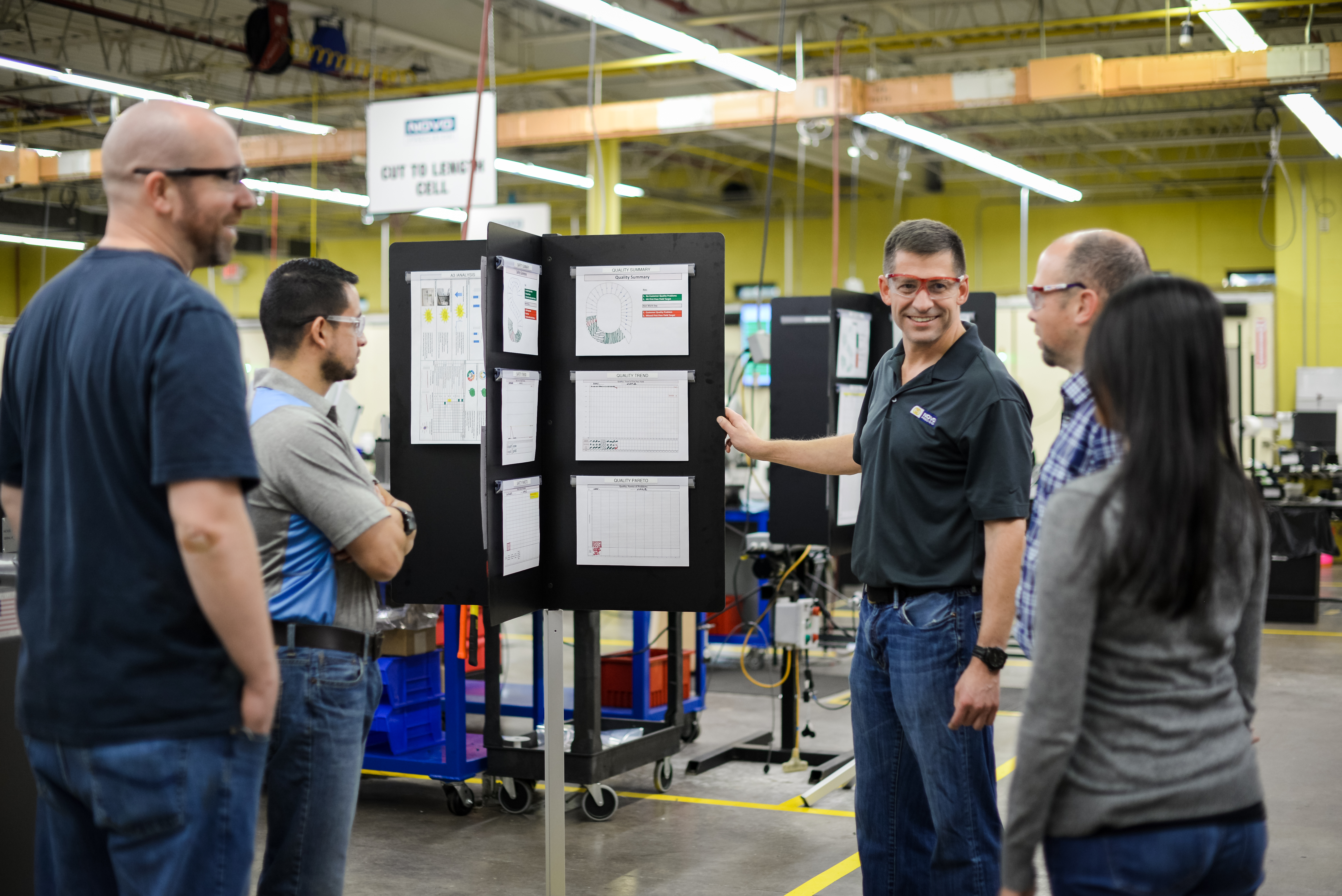
in a very small footprint. This stand can be configured to present any information that is relevant in a shop floor or office environment with a 60%+ reduction in floor space versus a standard white board and without needing a wall. We have designed a professional solution that is turn-key with minor assembly required that looks great on a shop floor or in any environment.
The original purpose of the product was to assist in creating a turn-key solution for implementing a Shop Floor or Gemba Walk. Included in the package we will provide all the basic forms and training material for you to perform a daily Shop Floor or Gemba Walk. This is an incredibly powerful tool in driving organizational alignment and driving improved operational performance. We can also provide training to support companies in implementation.
Companies Using Lean Metrics Stand:
Visual Metrics System Part List
Product Detail
(1) Upper Extrusion
(1) Lower Extrusion
(1) Base Unit
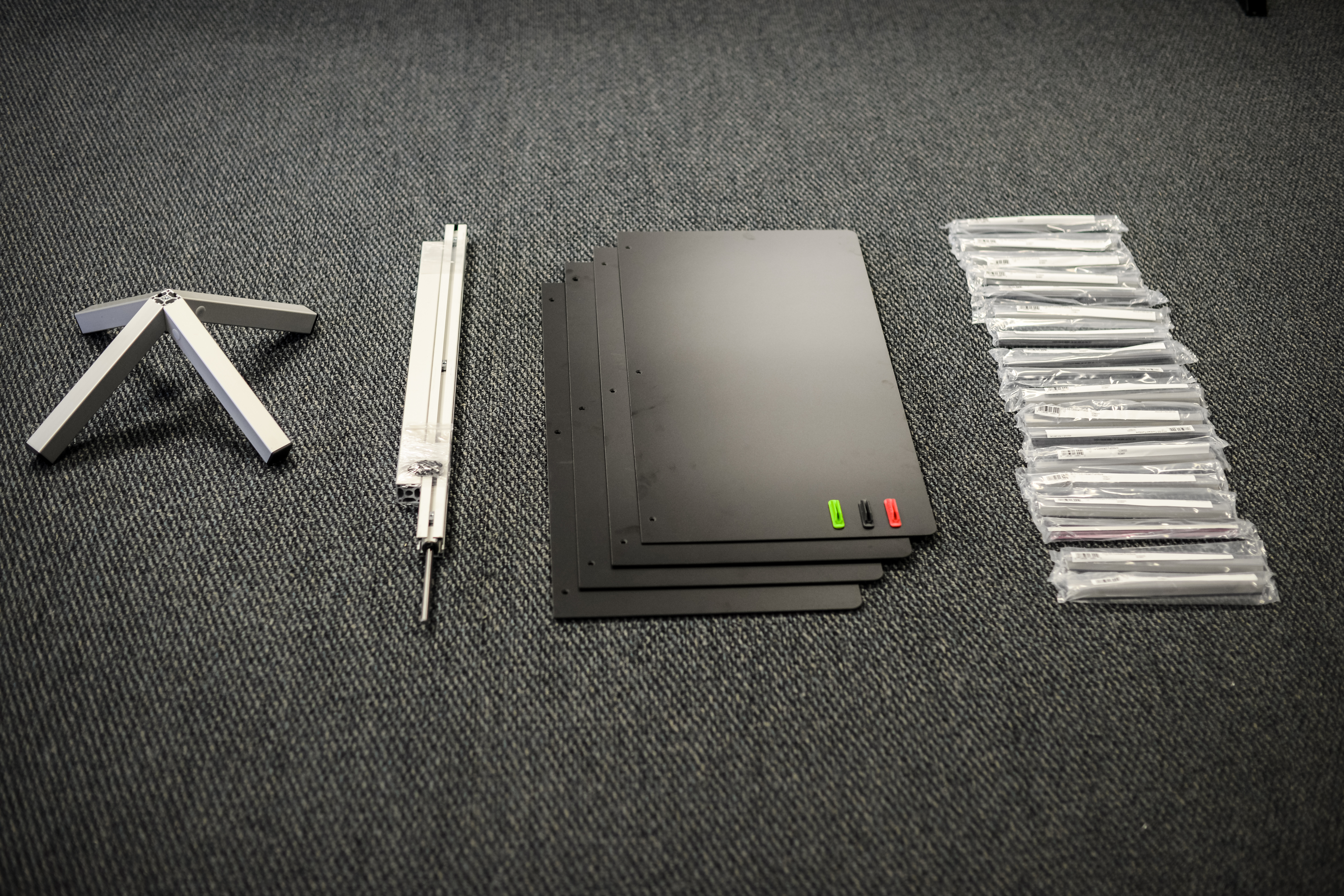
(1) Pivot Bearing Assembly
(4) Dry-Erase Panels (White or Black available)
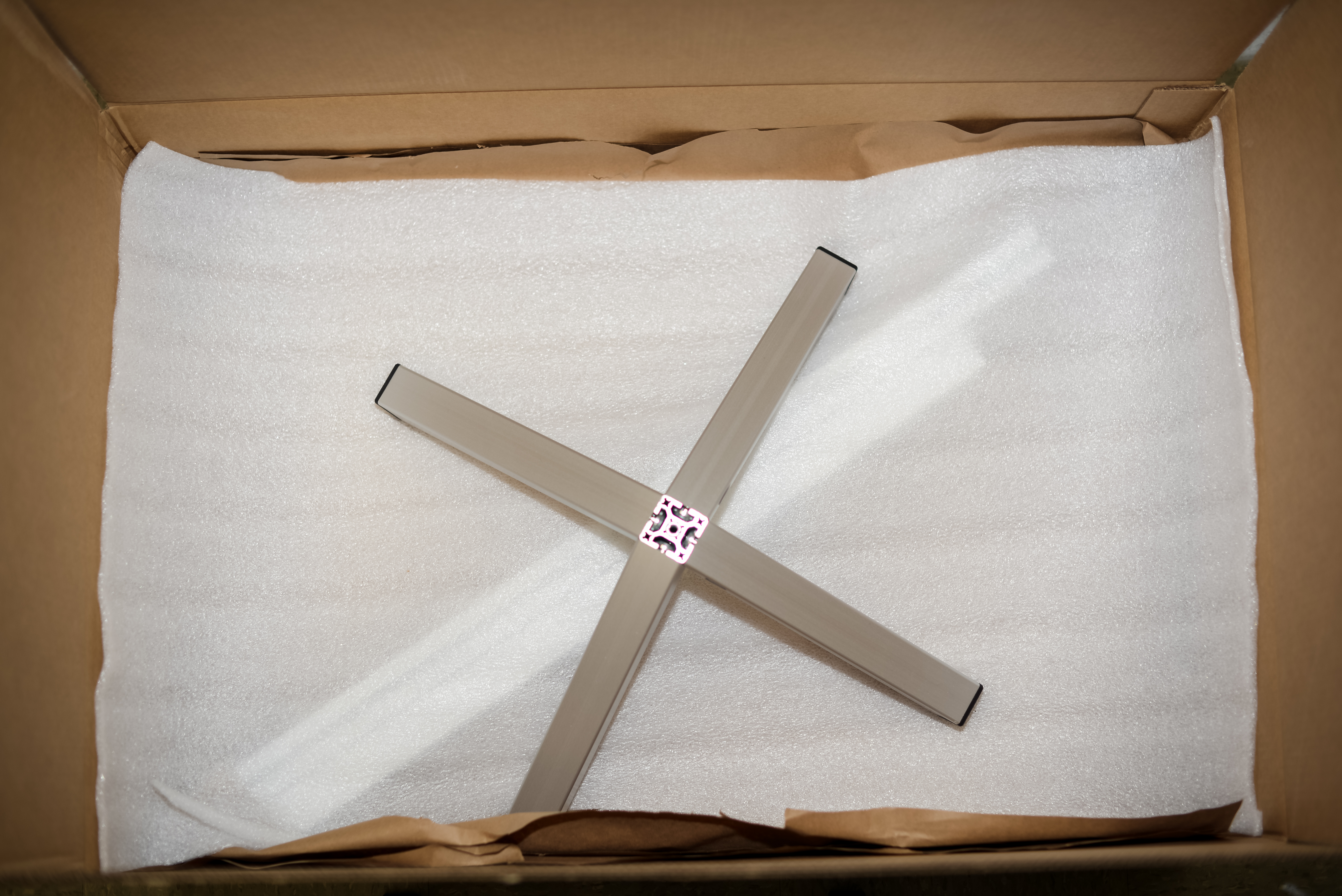
(1) Hardware Kit
(3) Pen Pal Pen Holders (1) red, (1) green and (1) black)
Options Include
-Clipholders (rail style)
*Requires 3mm Hex Key and 5/32 Hex Key (not included)
**Recommended Level & Tape Measure
Improve Shop Floor Performance in 2018
At Novo Precision we are announcing the release of a new product called our Lean Metrics Stand. This is a very professional tool for presenting information which can be used for Gemba / Shop Floor Walk. The rotating board does not require a wall and consumes 40% of the space than a traditional whiteboard. This tool will greatly improve your shop floor management and performance by setting clear targets, measuring performance, identifying biggest issues, driving improvements, and looks very sharp. We provide the this as a turnkey system with the board, performance metrics, and recommended approach to quickly implement and generate business impact.
Lean Manufacturing Blog
Check out our six part series of Blogs created by Bill Hazard that will provide a step by step tutorial on transforming your shop through SQDCM and the use of metrics boards.
- Blog 1-Management Cadence
- Blog 2-Gemba or Shop Floor Walk
Metric Stand Summary
What we are offering is a very professional information stand that can be used to effectively present information or metrics in a very small footprint. This stand can be configured to present any information that is relevant in a shop floor or office environment with a 60%+ reduction in floor space versus a standard white board and without needing a wall. We have designed a professional solution that is turn-key with minor assembly required that looks great on a shop floor or in any environment.
The original purpose of the product was to assist in creating a turn-key solution for implementing a Shop Floor or Gemba Walk. Included in the package we will provide all the basic forms and training material for you to perform a daily Shop Floor or Gemba Walk. This is an incredibly powerful tool in driving organizational alignment and driving improved operational performance. We can also provide training to support companies in implementation.
Introduction
Over the last 20 years I have worked in manufacturing facilities around the world in consulting, managing operations, and currently as a company owner. In each of these roles I have worked with many great teams on a journey to transform companies from low level to significantly higher-level operations. This transition requires the right leadership that has a vision and the capability to communicate, align, and lead their teams toward an operational vision. There is not one right way to make this transition but there are some common themes that you see in higher level operations including:
- Shop Floor Focus – This is where the value added work occurs and leadership needs to be engaged and support their people.
- Consistent Management Operating Cadence – Need to have a process for managing operations that has consistency & is quantitative.
One of the most valuable tools that I have seen in improving operations is the Daily Shop Floor Management Walk or Gemba Walk. The primary objectives of this walk include:
- Sets clear manufacturing objectives and keeps score.
- Gives Shop Floor Management and the Team ownership for area performance.
- Creates good understanding of what is happening on the shop floor which is reviewed by all functional areas.
- Helps in understanding problems and aligning resources to help address the problems.
- Gives a structure with a Management Cadence as well as to start drive continuous improvement.
There are always challenges in getting this implemented that are logistical as well as making it look professional. The purpose of this product is to give you a turn key system that in a matter of a few hours you can have assembled and functional on your shop floor. This will also save you a lot of cost in engineering and tool room resources in creating your own solution.
Basic Thinking
All production based companies should have a strategy for a continuous process improvement. In manufacturing – ‘What gets measured is what gets done!’ A universal method for this is the incremental process, PDCA (Plan-Do-Check- Act). PDCA is broken down by
One way to implement PDCA is through a daily shop floor walk where each production area reports out prior day performance to the leadership team. This can be tailored to the environment however we have developed a standard approach and physical components to help companies implement.
Objectives:
- Have Clear Operational Targets for each production area with a balanced approach around Safety, Quality, Delivery, Cost, and Morale (SQDCM).
- Area Management understands targets and performance which they report out daily in an efficient manner.
- Enables clear understanding of operational performance, issues impacting, and improvements being implemented.
- Creates level of accountability / urgency in addressing issues impacting performance.
- Allows all functional areas to understand and support operational performance through plan of action.
- Provides setting for management to coach functional areas.
Who:
- Company Leadership Team (All Functional Areas).
- Generally, will be the functional leads of Manufacturing Management, Engineering, Sales, Accounting, Maintenance, Purchasing, Human Resources.
When:
- Daily operational meetings should take place at a set time every day. Functional areas will have ample time to document performance metrics of the previous day in preparation for the meeting. It is recommended that that these meetings take place early in the day to allow for the previous day’s performance to be understood, analyzed, and acted upon.
Sample Agenda:
These will be customized based on the type business and needs of the business.
Example of our Morning Walk:
- Lead Preparation: Before each meeting the members of the leadership team that will be presenting their functional area’s current condition must prepare the necessary information. This is as easy as using green, black, and red markers to update the KPI boards out on the floor. The leadership team presenters must update their Metrics, Trends, Pareto’s, and Top 3 prior to meeting. (This should take less then 10 minutes.)
- Shipping: We start with shipping as this shows where the company stands with respect to customer demand:
- The goal is to make sure that all functional areas understand customer requirements and how we are doing in achieving these commitments.
- The scheduling lead discusses yesterday’s shipments, today’s planned shipments, shipments behind schedule, and any changes in shipment status. We look out 3 months for all 4 value streams.
- The scheduling lead will also review highest priorities by value stream.
- This will have to be designed to match your specific business.
- In general this part of the meeting should take no longer than 5 minutes.
- Production Areas: The production meetings update the leadership team as to where the company stands regarding production results:
- The Team of each area starts by summarizing yesterday’s production using the Prior Day Production Analysis Board – Summarizing any problems that were experienced:
- In the example provided notice how the hourly production results are written in green when the production meets or exceeds the listed hourly plan, or it is written in red when production does not meet the listed hourly plan. The cumulative production results are written green when production is equal to or greater than the cumulative plan at that point in time, or it is written in red when cumulative production does not meet its plan.
- Reviews if achieved Safety Goals – If Red then will review Trend & Pareto data
- Reviews if achieved Quality Goals – If Red then will review Trend & Pareto data
- Reviews if achieved Delivery Goals – If Red then will review Trend & Pareto data
- Reviews if achieved Cost Goals – If Red then will review Trend & Pareto data
- Reviews if achieved Morale Goals – If Red then will review Trend & Pareto data
- Reviews status of Top 3 Focus Improvements
- Open Discussion if any questions from Leadership Team.
- The Team of each area starts by summarizing yesterday’s production using the Prior Day Production Analysis Board – Summarizing any problems that were experienced:
(This is repeated for each production Area)
- Leadership Team Review:
- Review of monthly shipping walk – how are we progressing to monthly Sales Targets
- We have a quick leadership review:
- Any general business highlights
- Any visits today.
- Review any focus areas for the Team